The impact of 3D printing on manufacturing in 2025
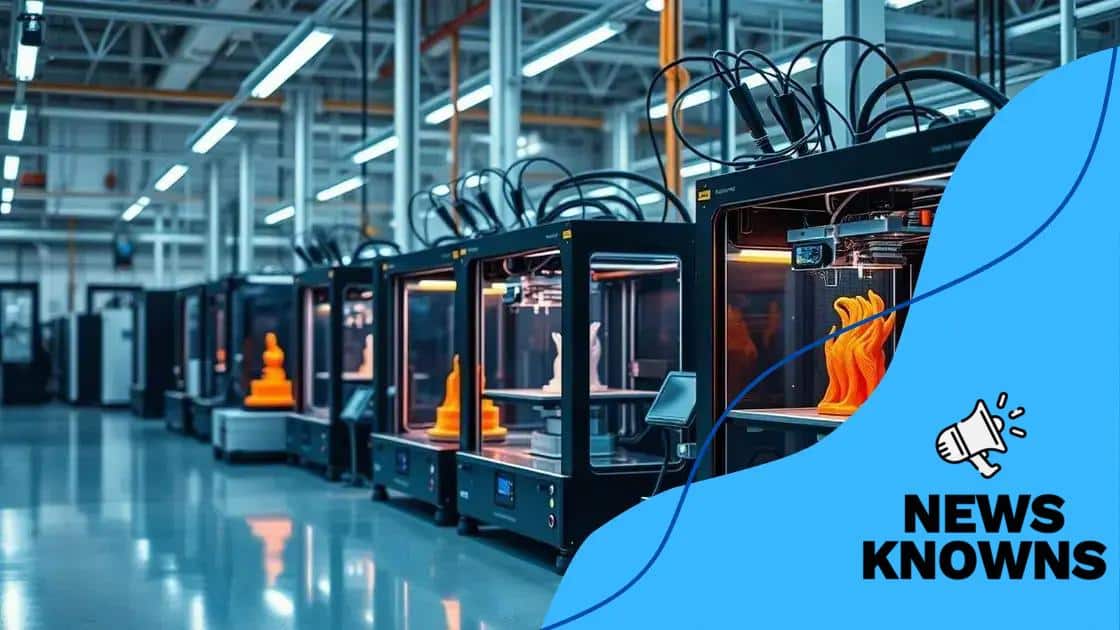
The impact of 3D printing on manufacturing in 2025 includes advancements in sustainable materials, increased automation, and the ability to create customized products, significantly enhancing efficiency and innovation across various industries.
The impact of 3D printing on manufacturing in 2025 is set to reshape the way we create products. Have you thought about how this technology might influence your industry? Let’s dive into its potential.
Overview of 3D printing technology
3D printing technology is changing how we produce items. This innovative process allows for the creation of complex shapes quickly and efficiently. Let’s explore its core components and benefits.
What is 3D Printing?
At its core, 3D printing involves creating three-dimensional objects from digital files. The printer adds material layer by layer until the final product is completed. This method contrasts with traditional manufacturing, which often requires cutting away material.
Benefits of 3D Printing
- Flexibility in design and customization
- Reduction in waste materials
- Speeding up the production process
- Cost-effective for small production runs
The flexibility of 3D printing technology is remarkable. Designers can easily modify digital files to create unique products tailored to specific needs. This adaptability is beneficial in various fields, including healthcare, automotive, and consumer products.
Types of 3D Printing Technologies
Several methods exist within 3D printing, each with its strengths:
- Fused Deposition Modeling (FDM): uses thermoplastic materials.
- Stereolithography (SLA): relies on resin and UV light.
- Selective Laser Sintering (SLS): combines powdered materials.
Understanding these different types helps industries choose the right method for their applications. Each technology caters to specific needs and challenges.
In summary, 3D printing technology stands out for its versatility and efficiency. As it continues to evolve, industries will find even more innovative applications that can streamline production and reduce costs.
Advancements in materials and techniques
Recent advancements in materials and techniques are pushing the limits of 3D printing technology. These innovations have made it possible to create stronger, lighter, and more complex structures than ever before.
New Materials in 3D Printing
Modern 3D printing now uses a variety of materials that were not previously available. From metals to flexible plastics, the choice is vast. This variety allows for applications in diverse industries.
- Metals: Used for aerospace and medical implants.
- Bioplastics: Eco-friendly options for consumer products.
- Composites: Combined materials for enhanced performance.
The introduction of these new materials is significant. Manufacturers can now design parts that are not only functional but also aesthetically pleasing.
Techniques Enhancing Printing Efficiency
Besides materials, techniques have also improved. For instance, multi-material printing enables integration of different substances in a single print. This results in components with varied properties in one piece.
Additionally, technologies like digital light processing (DLP) and binder jetting have vastly increased printing speed and precision. These advancements make it feasible to produce large batches of items quickly.
As materials and techniques advance, the future of 3D printing continues to evolve. This evolution opens opportunities for creating products that were previously unimaginable, impacting everything from design to function.
How industries are adapting to 3D printing
Industries around the world are quickly adapting to 3D printing. This technology is becoming essential for businesses that want to stay competitive. Companies are discovering new ways to integrate 3D printing into their manufacturing processes.
Adoption in Different Markets
From healthcare to automotive, various sectors are utilizing 3D printing for unique applications. In healthcare, for example, doctors are creating custom prosthetics and implants.
- Aerospace: Lightweight parts reduce fuel consumption.
- Automotive: Fast prototyping speeds up the design process.
- Consumer Products: Personalized items attract more customers.
These real-world applications showcase how 3D printing can solve challenges specific to each industry.
Streamlining Production Processes
Many companies have found that adopting 3D printing leads to streamlined production. The ability to produce complex designs without the need for molds or tooling saves time and resources.
Moreover, on-demand production reduces the need for inventory. This means businesses can respond more swiftly to market demands.
Another significant shift is the collaboration between companies and 3D printing service providers. This partnership allows businesses to leverage expertise and technologies they might not possess in-house.
As industries continue to innovate, the use of 3D printing will likely expand further. Companies need to stay informed and proactive to harness its full potential.
Case studies of successful implementations
Several companies across various industries have successfully implemented 3D printing technologies. These case studies showcase how businesses are leveraging this innovation to improve their products and processes.
Healthcare Innovations
A notable case in healthcare is a hospital that started using 3D printing to create custom surgical models. Surgeons can now practice complex procedures on these models before performing actual surgeries. This prepares them better and can lead to quicker recovery times for patients.
- Custom implants: Tailored for individual patients.
- Prosthetics: Affordable, personalized solutions enhance quality of life.
- Anatomical models: Improve surgical outcomes.
The results have been remarkable, demonstrating how 3D printing can improve patient care.
Automotive Advancements
In the automotive sector, a leading car manufacturer adopted 3D printing to reduce lead times for prototyping. Instead of waiting weeks for traditional parts, they can now print components in a matter of days. This agility allows for faster design iterations and enhances innovation.
Furthermore, they have started using additive manufacturing for parts that are lighter yet strong, improving overall vehicle performance.
Aerospace Efficiency
The aerospace industry benefits greatly from 3D printing. A major aerospace company successfully implemented it to produce lightweight components that help reduce fuel consumption and lower emissions. By utilizing additive techniques, they can manufacture complex geometries that were once impossible.
Cases like these highlight that 3D printing is not just a trend; it is transforming how products are designed and produced, driving significant efficiency and effectiveness in multiple sectors.
Future trends in 3D printing for manufacturing
As technology evolves, the future trends in 3D printing for manufacturing are becoming clearer. Companies are beginning to embrace new innovations that promise to revolutionize the way products are made.
Increased Use of Sustainable Materials
One significant trend is the growing focus on sustainability. Manufacturers are now exploring eco-friendly materials for 3D printing. This includes bioplastics and recycled materials, which reduce waste and environmental impact.
- Reduced carbon footprint: Eco-friendly materials help fight climate change.
- Circular economy: Using recycled products promotes sustainability.
- Innovation: New materials are developed, offering more choices.
As a result, companies can maintain product quality while being environmentally responsible.
Advancements in Software and Automation
The evolution of software tools is another key trend. Companies are investing in advanced software that integrates artificial intelligence to optimize 3D printing processes. Automation will streamline production lines, making them faster and more efficient.
In addition, simulation software allows designers to visualize outcomes before printing. This capability reduces errors and ensures that the final products meet specifications.
Mass Customization and Personalization
Another fascinating trend is the shift toward mass customization. 3D printing enables manufacturers to create personalized items at scale. This trend is particularly evident in consumer products, healthcare, and fashion.
Companies can now tailor products based on individual customer preferences, leading to an enhanced user experience. This level of personalization builds stronger connections between brands and consumers.
Overall, the future of 3D printing in manufacturing shows great promise. These emerging trends will likely result in improved processes, reduced waste, and better customer satisfaction, setting the foundation for a more innovative industry.
The conclusion emphasizes that the future of 3D printing in manufacturing is bright and full of potential. As technology continues to innovate, industries will see exciting advancements in sustainable materials, increased automation, and greater customization. These trends not only improve manufacturing efficiency but also enhance customer experiences. The journey of 3D printing is just beginning, and its impact will shape the way products are created and designed in the years to come.
FAQ – Frequently Asked Questions About 3D Printing in Manufacturing
What are the main benefits of using 3D printing in manufacturing?
3D printing offers benefits such as reduced waste, faster prototyping, and the ability to create complex designs that are difficult with traditional methods.
How is sustainability impacting 3D printing materials?
Sustainability is leading to the development of eco-friendly materials, like bioplastics and recycled substances, which minimize environmental impact.
What role does automation play in 3D printing?
Automation enhances efficiency by streamlining production processes, reducing manual errors, and speeding up manufacturing timelines.
Can 3D printing be used for mass customization?
Yes, 3D printing allows for mass customization, enabling manufacturers to create personalized products tailored to individual customer preferences.